Have you ever wondered what exactly an industrial mixer is? These powerful machines are used in a variety of industries to mix, blend, and process materials. They come in a variety of sizes and configurations, and can be used to mix a wide range of materials, from liquids to solids.
Editor’s Note: This guide to industrial mixers was last published on [date].
Because we understand how important it is to make the right decision, our team of experts has analyzed and compared the top industrial mixers on the market. The result is this comprehensive guide, which provides everything you need to know about these machines.
Industrial Mixer
Industrial mixers are essential pieces of equipment in a variety of industries. They are used to mix, blend, and process materials, and come in a variety of sizes and configurations. Here are seven key aspects of industrial mixers:
- Type: Industrial mixers can be classified into several types, including batch mixers, continuous mixers, and inline mixers.
- Size: Industrial mixers can range in size from small, portable units to large, industrial-scale machines.
- Capacity: The capacity of an industrial mixer is determined by the volume of material it can hold and process.
- Speed: The speed of an industrial mixer is measured in revolutions per minute (RPM) and determines how quickly the materials are mixed.
- Power: The power of an industrial mixer is measured in horsepower (HP) and determines how much torque the mixer can generate.
- Materials of construction: Industrial mixers can be made from a variety of materials, including stainless steel, carbon steel, and plastic.
- Features: Industrial mixers can come with a variety of features, such as variable speed control, temperature control, and automation.
These are just a few of the key aspects of industrial mixers. When choosing an industrial mixer, it is important to consider the specific needs of your application. By understanding the different types, sizes, capacities, speeds, powers, materials of construction, and features of industrial mixers, you can choose the right machine for your job.
Type
The type of industrial mixer you choose will depend on the specific needs of your application. Batch mixers are ideal for mixing small batches of material, while continuous mixers are better suited for mixing large batches of material. Inline mixers are used to mix materials as they are being processed.
Here is a table that summarizes the key differences between batch mixers, continuous mixers, and inline mixers:
| Type of Mixer | Description | Advantages | Disadvantages ||—|—|—|—|| Batch Mixer | Mixes materials in a batch process | Can handle a variety of materials | Can be slow and inefficient || Continuous Mixer | Mixes materials in a continuous process | Can handle large batches of material | Can be expensive and complex || Inline Mixer | Mixes materials as they are being processed | Can be used to mix a variety of materials | Can be difficult to control |
By understanding the different types of industrial mixers, you can choose the right machine for your job.
Size
The size of an industrial mixer is an important factor to consider when choosing the right machine for your application. Small, portable mixers are ideal for mixing small batches of material, while large, industrial-scale mixers are better suited for mixing large batches of material. The size of the mixer will also determine the power and capacity of the machine.
Here are some examples of the different sizes of industrial mixers available:
| Size | Capacity | Power ||—|—|—|—|| Small | Up to 5 gallons | Up to 1 horsepower || Medium | 5 to 50 gallons | 1 to 5 horsepower || Large | Over 50 gallons | Over 5 horsepower |
When choosing the right size industrial mixer for your application, it is important to consider the following factors:
- The volume of material you need to mix
- The type of material you need to mix
- The speed at which you need to mix the material
- The power you need to mix the material
By understanding the different sizes of industrial mixers available and the factors to consider when choosing a mixer, you can choose the right machine for your job.
Capacity
The capacity of an industrial mixer is a key factor to consider when choosing the right machine for your application. The capacity of a mixer is measured in gallons or liters, and it determines the amount of material that the mixer can hold and process at one time.
- Mixing large batches: If you need to mix large batches of material, you will need an industrial mixer with a large capacity. Large-capacity mixers can hold and process hundreds of gallons of material at a time.
- Mixing small batches: If you only need to mix small batches of material, you can get away with a smaller mixer. Small-capacity mixers can hold and process just a few gallons of material at a time.
- Mixing different types of materials: The capacity of an industrial mixer can also be affected by the type of material you are mixing. Some materials, such as liquids, are easier to mix than others, such as solids. If you are mixing a difficult-to-mix material, you will need a mixer with a larger capacity.
- Mixing speed: The capacity of an industrial mixer can also be affected by the speed at which you need to mix the material. If you need to mix the material quickly, you will need a mixer with a higher capacity.
By understanding the factors that affect the capacity of an industrial mixer, you can choose the right machine for your application. A properly sized mixer will help you to mix your materials quickly and efficiently.
Speed
The speed of an industrial mixer is a critical factor in determining how quickly and efficiently materials can be mixed. Measured in revolutions per minute (RPM), the speed of an industrial mixer directly affects the mixing process and the end result.
- Mixing Time: The speed of an industrial mixer has a direct impact on mixing time. Higher speeds result in shorter mixing times, as the materials are agitated more vigorously and blended more quickly. This is especially important in applications where time is a critical factor, such as in manufacturing processes with tight deadlines.
- Mixing Quality: The speed of an industrial mixer also affects the quality of the mixing process. Higher speeds can help to create a more homogeneous mixture, as the materials are more thoroughly blended together. This is important in applications where a consistent and uniform mixture is required, such as in the production of pharmaceuticals or food products.
- Energy Consumption: The speed of an industrial mixer can also impact energy consumption. Higher speeds require more energy to operate, as the motor must work harder to rotate the mixing blades. This is an important consideration in applications where energy efficiency is a priority, such as in large-scale manufacturing or processing operations.
- Wear and Tear: The speed of an industrial mixer can also affect the wear and tear on the machine. Higher speeds can put more stress on the motor, bearings, and other components, leading to increased wear and tear over time. This is an important consideration in applications where the mixer is used frequently or for extended periods of time.
By understanding the relationship between speed and the mixing process, manufacturers can optimize the operation of their industrial mixers to achieve the desired results. Selecting the appropriate speed for the specific application can help to improve mixing time, quality, energy consumption, and equipment longevity.
Power
The power of an industrial mixer is a critical factor in determining its ability to mix different materials. Measured in horsepower (HP), the power of an industrial mixer directly affects the mixing process and the end result.
Here’s how the power of an industrial mixer is connected to its functionality:
- Mixing Heavy Materials: The power of an industrial mixer is crucial when mixing heavy or viscous materials. A higher horsepower motor can generate more torque, which is necessary to overcome the resistance of these materials and achieve a thorough mix.
- Mixing Large Batches: Industrial mixers with higher power are better suited for mixing large batches of materials. A more powerful motor can handle the increased load and maintain consistent mixing throughout the batch.
- Mixing Time: The power of an industrial mixer also affects the mixing time. A higher horsepower motor can rotate the mixing blades faster, reducing the time it takes to achieve a homogeneous mixture.
- Energy Efficiency: While higher power industrial mixers can provide faster mixing times, they also consume more energy. It’s important to consider the energy efficiency of the mixer in relation to the specific mixing requirements.
By understanding the connection between power and the mixing process, manufacturers can select the right industrial mixer for their specific applications. A properly powered mixer will ensure efficient mixing, reduced mixing times, and optimal results.
Table: Power and Mixing Capabilities of Industrial Mixers
Horsepower (HP) | Mixing Capabilities |
---|---|
1-5 HP | Suitable for mixing small batches of light to medium-weight materials |
5-10 HP | Ideal for mixing medium-sized batches of medium to heavy-weight materials |
10-20 HP | Designed for mixing large batches of heavy or viscous materials |
20+ HP | Used for industrial-scale mixing applications involving large volumes of heavy or challenging materials |
Materials of construction
The materials used in the construction of industrial mixers play a crucial role in determining their performance, durability, and suitability for different mixing applications. Industrial mixers can be made from a variety of materials, each with its own unique properties and advantages:
- Stainless steel: Stainless steel is a popular choice for industrial mixers due to its excellent corrosion resistance, durability, and ease of cleaning. It is commonly used in food processing, pharmaceutical, and chemical industries where hygiene and contamination control are critical.
- Carbon steel: Carbon steel is a strong and cost-effective material that is often used in industrial mixers for heavy-duty applications. It is less resistant to corrosion than stainless steel, but it is more affordable and can withstand higher temperatures.
- Plastic: Plastic is a lightweight and corrosion-resistant material that is often used in industrial mixers for mixing light to medium-viscosity materials. It is also a good choice for applications where electrical insulation is required.
The choice of material for an industrial mixer depends on a number of factors, including the type of materials being mixed, the operating environment, and the desired performance characteristics. By understanding the properties and advantages of different materials, manufacturers can select the right industrial mixer for their specific application.
Features
Industrial mixers are versatile machines that can be enhanced with a range of features to meet the specific demands of different mixing applications. Variable speed control, temperature control, and automation are among the most common and impactful features available.
Variable speed control allows operators to adjust the mixing speed to suit the characteristics of the materials being mixed. This is particularly important for applications where different materials or viscosities require different mixing speeds to achieve optimal results. Variable speed control also enables operators to fine-tune the mixing process for improved efficiency and product quality.
Temperature control is another important feature for industrial mixers, especially in applications where temperature plays a critical role in the mixing process. By precisely controlling the temperature of the mixing vessel, operators can ensure that the materials are mixed at the optimal temperature for desired outcomes. Temperature control systems can be integrated with sensors and feedback loops to maintain consistent temperatures throughout the mixing process.
Automation is a valuable feature for industrial mixers, particularly in large-scale or continuous mixing operations. Automated mixers can be programmed to follow specific mixing recipes, reducing the need for manual intervention and improving consistency. Automation also enables remote monitoring and control of the mixing process, allowing operators to manage multiple mixers from a central location.
The combination of features such as variable speed control, temperature control, and automation enhances the versatility and effectiveness of industrial mixers. By carefully considering the features required for a specific application, manufacturers can select the right industrial mixer to optimize their mixing processes and achieve desired outcomes.
Table: Features and Benefits of Industrial Mixer Features
Feature | Benefits |
---|---|
Variable speed control | – Adjust mixing speed to suit material characteristics- Optimize mixing efficiency and product quality |
Temperature control | – Maintain optimal mixing temperature- Ensure consistent product quality- Prevent thermal damage to materials |
Automation | – Reduce manual intervention and improve consistency- Enable remote monitoring and control- Increase productivity and efficiency |
Industrial Mixer FAQs
This section addresses frequently asked questions (FAQs) about industrial mixers, providing concise and informative answers to common concerns and misconceptions.
Question 1: What are the different types of industrial mixers available?
Answer: Industrial mixers come in various types, including batch mixers for smaller quantities, continuous mixers for larger volumes, and inline mixers for incorporating materials directly into a process line.
Question 2: How do I choose the right size of industrial mixer for my needs?
Answer: The appropriate size depends on factors like the volume and type of materials being mixed, as well as the desired mixing speed and efficiency.
Question 3: What materials are commonly used in the construction of industrial mixers?
Answer: Industrial mixers are typically made from materials like stainless steel for durability and corrosion resistance, carbon steel for strength and affordability, or plastic for lightweight and corrosion resistance.
Question 4: What features should I look for in an industrial mixer?
Answer: Important features include variable speed control for adjusting mixing intensity, temperature control for maintaining optimal conditions, and automation for efficient and consistent operation.
Question 5: How do I ensure the safety of an industrial mixer?
Answer: Safety measures include proper installation, regular maintenance, using appropriate guards, and following safety protocols to minimize risks.
Question 6: What are the benefits of using an industrial mixer?
Answer: Industrial mixers offer advantages such as improved mixing efficiency, consistent product quality, reduced labor costs, and increased productivity.
Summary: Understanding the different types, sizes, materials, features, safety considerations, and benefits of industrial mixers is crucial for selecting the right equipment for specific mixing requirements.
Transition: For further information on industrial mixers, their applications, and specific models available in the market, please explore the rest of our website.
Industrial Mixer Tips
Industrial mixers play a crucial role in various industries by efficiently blending and processing materials. To optimize their performance and ensure effective mixing, consider the following tips:
Tip 1: Choose the Right Mixer Type:
Select the appropriate mixer type based on your specific mixing requirements. Batch mixers are suitable for small volumes, continuous mixers for large-scale operations, and inline mixers for adding ingredients directly into a process line.
Tip 2: Determine Optimal Size:
Consider the volume and characteristics of materials being mixed when determining the mixer size. A correctly sized mixer ensures efficient mixing and prevents overloading or underutilization.
Tip 3: Select Durable Materials:
Choose mixers constructed from durable materials such as stainless steel for corrosion resistance, carbon steel for strength, or plastic for lightweight and corrosion resistance. The material should align with the specific mixing environment and materials being handled.
Tip 4: Consider Essential Features:
Look for mixers with essential features like variable speed control to adjust mixing intensity, temperature control to maintain optimal mixing conditions, and automation for efficient and consistent mixing operations.
Tip 5: Ensure Safety Measures:
Prioritize safety by ensuring proper installation, regular maintenance, and adherence to safety protocols. Use appropriate guards and follow established guidelines to minimize risks associated with industrial mixers.
Summary:
By following these tips, you can select and operate industrial mixers effectively, ensuring efficient mixing processes, consistent product quality, and enhanced productivity.
Transition:
For further insights into industrial mixers, including their applications and specific models available in the market, explore the rest of our website.
Industrial Mixer
Industrial mixers have emerged as indispensable tools across various industries, offering efficient and reliable mixing solutions. This comprehensive guide has explored the key aspects of industrial mixers, encompassing their types, sizes, materials, features, and safety considerations.
By understanding the specific requirements of your mixing application, you can select the optimal industrial mixer that aligns with your needs. Whether it’s a batch mixer for small-scale operations, a continuous mixer for large-volume processing, or an inline mixer for seamless integration into production lines, there’s an industrial mixer suited to every application.
Remember, the choice of materials, such as stainless steel, carbon steel, or plastic, should be guided by the mixing environment and the characteristics of the materials being handled. Additionally, essential features like variable speed control, temperature control, and automation can significantly enhance the efficiency and precision of your mixing processes.
Prioritizing safety is paramount when operating industrial mixers. Proper installation, regular maintenance, and adherence to safety protocols ensure a safe and productive work environment. By following these guidelines, you can harness the full potential of industrial mixers and achieve optimal mixing outcomes.
As technology continues to advance, industrial mixers are poised to become even more sophisticated and efficient. With the integration of automation, real-time monitoring, and advanced controls, the future of industrial mixing holds exciting possibilities for enhanced productivity and process optimization.
Youtube Video:
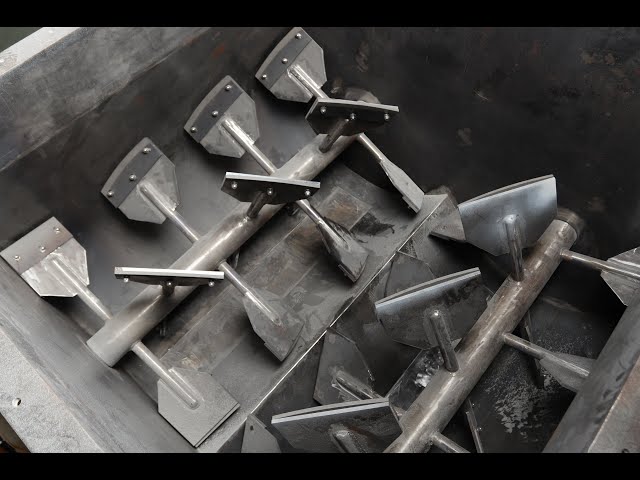