What is an industrial miller welder? Industrial miller welders are high-powered welding machines designed for heavy-duty welding applications in industrial settings.
Editor’s Note: This article on “industrial miller welders” was published on [today’s date]. This topic is important to read because it provides valuable insights into the world of industrial welding and the role of miller welders in this industry.
After analyzing different types of industrial welders and digging information from various resources, we have put together this guide to help you make the right decision.
Key Differences:
Feature | Industrial Miller Welder |
---|---|
Power | High-powered |
Duty Cycle | Heavy-duty |
Applications | Industrial welding |
Main Article Topics:
- Types of Industrial Miller Welders
- Benefits of Using Industrial Miller Welders
- Factors to Consider When Choosing an Industrial Miller Welder
- Tips for Using Industrial Miller Welders Safely
Industrial Miller Welders
Industrial miller welders are essential tools for heavy-duty welding applications in industrial settings. Here are six key aspects to consider when using industrial miller welders:
- Power: Industrial miller welders are high-powered machines, capable of welding thick metals and performing demanding welding tasks.
- Duty Cycle: These welders have a high duty cycle, meaning they can be used for extended periods without overheating.
- Durability: Industrial miller welders are built to last, with robust construction and durable components.
- Versatility: They can be used for a variety of welding applications, including MIG, TIG, and stick welding.
- Safety: Industrial miller welders are equipped with safety features to protect the user, such as fume extraction systems and protective shields.
- Reliability: These welders are known for their reliability and consistent performance, even in demanding industrial environments.
These key aspects make industrial miller welders an essential tool for any industrial welding application. They provide the power, durability, and versatility needed to get the job done right.
Power
Industrial miller welders are known for their high power output, which enables them to weld thick metals and perform demanding welding tasks. This power is essential for industrial applications, where welders need to be able to join thick pieces of metal together quickly and efficiently.
- High amperage output: Industrial miller welders can produce high amperage output, which is necessary for welding thick metals. Amperage is a measure of the amount of electrical current flowing through the welder, and it determines the heat and penetration of the weld.
- Fast welding speeds: The high power output of industrial miller welders also allows them to weld at fast speeds. This is important for industrial applications, where time is money.
- Variety of welding processes: Industrial miller welders can be used for a variety of welding processes, including MIG, TIG, and stick welding. This versatility makes them a valuable tool for any industrial welding shop.
The high power output of industrial miller welders makes them an essential tool for any industrial welding application. They provide the power, durability, and versatility needed to get the job done right.
Duty Cycle
Industrial miller welders are known for their high duty cycle. This means that they can be used for extended periods without overheating. This is an important factor for industrial applications, where welders need to be able to work for long periods of time without having to stop and wait for the welder to cool down.
- Continuous welding: Industrial miller welders can be used for continuous welding, which is necessary for long welding jobs. This means that welders can work without having to stop and wait for the welder to cool down.
- Increased productivity: The high duty cycle of industrial miller welders allows welders to work more efficiently and productively. This can lead to increased productivity and cost savings for businesses.
- Reduced downtime: The high duty cycle of industrial miller welders also reduces downtime. This is because welders do not have to stop and wait for the welder to cool down as often.
The high duty cycle of industrial miller welders makes them an essential tool for any industrial welding application. They provide the power, durability, and versatility needed to get the job done right.
Durability
The durability of industrial miller welders is a key factor in their popularity and success in industrial settings. These welders are built to withstand the rigors of heavy-duty welding applications, and they can provide years of reliable service.
There are several factors that contribute to the durability of industrial miller welders. First, these welders are typically made from high-quality materials, such as steel and aluminum. This ensures that they can withstand the heat and stress of welding without warping or breaking.
Second, industrial miller welders are often equipped with robust construction features, such as reinforced frames and heavy-duty components. This helps to protect the welder from damage, even in the most demanding environments.
Finally, industrial miller welders are often designed with features that extend their lifespan. For example, many models have built-in cooling systems that help to prevent the welder from overheating. This can help to prevent damage to the welder’s components and extend its lifespan.
The durability of industrial miller welders is a key benefit for businesses that use them. These welders can provide years of reliable service, which can save businesses money in the long run.
Versatility
The versatility of industrial miller welders is one of their key benefits. They can be used for a wide range of welding applications, including MIG, TIG, and stick welding. This makes them a valuable tool for any industrial welding shop.
MIG welding is a popular choice for industrial applications because it is fast and efficient. TIG welding is often used for more delicate welding tasks, such as welding thin metals or welding in tight spaces. Stick welding is a versatile welding process that can be used for a variety of applications, including welding thick metals and welding in outdoor environments.
The versatility of industrial miller welders makes them a valuable tool for any industrial welding shop. They can be used for a wide range of welding applications, and they can provide years of reliable service.
Here are some examples of how industrial miller welders are used in different industries:
- In the automotive industry, industrial miller welders are used to weld car bodies, frames, and other components.
- In the construction industry, industrial miller welders are used to weld structural steel, piping, and other components.
- In the shipbuilding industry, industrial miller welders are used to weld ships’ hulls, decks, and other components.
- In the oil and gas industry, industrial miller welders are used to weld pipelines, storage tanks, and other components.
These are just a few examples of the many industries that use industrial miller welders. These welders are a versatile tool that can be used for a wide range of welding applications.
Safety
Industrial miller welders are designed with safety features to protect the user from harmful fumes and sparks. These features include fume extraction systems and protective shields.
- Fume Extraction Systems: Fume extraction systems remove harmful fumes from the welding area, protecting the user from inhaling these fumes. Fumes can contain dangerous gases and particles that can cause respiratory problems and other health issues.
- Protective Shields: Protective shields protect the user’s eyes and skin from sparks and other hazards. Sparks can cause burns and eye damage, and protective shields help to prevent these injuries.
These safety features are essential for protecting the user from the hazards of welding. By using industrial miller welders with these safety features, users can help to ensure their safety and well-being.
Reliability
Reliability is a key factor to consider when choosing an industrial miller welder. Industrial environments can be harsh and demanding, and welders need to be able to rely on their equipment to perform consistently, even under these conditions.
Industrial miller welders are known for their reliability and consistent performance. They are built to withstand the rigors of industrial use, and they can provide years of trouble-free service.
Here are some examples of how industrial miller welders are used in demanding industrial environments:
- In the automotive industry, industrial miller welders are used to weld car bodies, frames, and other components. These welders must be able to withstand the high heat and heavy use that is common in automotive manufacturing.
- In the construction industry, industrial miller welders are used to weld structural steel, piping, and other components. These welders must be able to withstand the outdoor elements and the harsh conditions of construction sites.
- In the shipbuilding industry, industrial miller welders are used to weld ships’ hulls, decks, and other components. These welders must be able to withstand the saltwater environment and the high winds and waves that are common at sea.
These are just a few examples of the many demanding industrial environments where industrial miller welders are used. These welders are known for their reliability and consistent performance, and they can provide years of trouble-free service.
When choosing an industrial miller welder, it is important to consider the reliability of the welder. Industrial miller welders are known for their reliability and consistent performance, and they can provide years of trouble-free service.
FAQs on Industrial Miller Welders
This section provides answers to frequently asked questions about industrial miller welders. These FAQs are designed to help you understand the key features and benefits of these welders, and to help you make an informed decision about whether an industrial miller welder is right for your needs.
Question 1: What are the key features of industrial miller welders?
Industrial miller welders are known for their power, durability, versatility, safety, and reliability. They are designed for heavy-duty welding applications in industrial settings, and they can provide years of trouble-free service.
Question 2: What are the benefits of using industrial miller welders?
Industrial miller welders offer a number of benefits, including:
- High power output for welding thick metals and performing demanding welding tasks
- High duty cycle for continuous welding without overheating
- Durability for withstanding the rigors of industrial use
- Versatility for use with a variety of welding processes
- Safety features to protect the user from harmful fumes and sparks
- Reliability for consistent performance in demanding industrial environments
Question 3: What are the different types of industrial miller welders?
Industrial miller welders are available in a variety of types, including:
- MIG welders
- TIG welders
- Stick welders
- Multi-process welders
Question 4: How do I choose the right industrial miller welder for my needs?
When choosing an industrial miller welder, it is important to consider the following factors:
- The type of welding you will be doing
- The thickness of the metal you will be welding
- The duty cycle you require
- The safety features you need
- The budget you have
Question 5: Where can I buy an industrial miller welder?
Industrial miller welders can be purchased from a variety of sources, including welding supply stores, online retailers, and hardware stores.
Question 6: How do I maintain an industrial miller welder?
To maintain an industrial miller welder, it is important to follow the manufacturer’s instructions. This includes regular cleaning and maintenance, as well as periodic inspections.
Industrial miller welders are a valuable tool for any industrial welding shop. They offer a number of benefits, including power, durability, versatility, safety, and reliability. When choosing an industrial miller welder, it is important to consider the type of welding you will be doing, the thickness of the metal you will be welding, the duty cycle you require, the safety features you need, and the budget you have.
Now that you know more about industrial miller welders, you can make an informed decision about whether one is right for your needs.
Tips for Using Industrial Miller Welders
Industrial miller welders are powerful and versatile tools, but they can also be dangerous if not used properly. Here are some tips to help you use industrial miller welders safely and effectively:
Tip 1: Always wear proper safety gear. This includes a welding helmet, gloves, and clothing that covers your skin.
Tip 2: Make sure your work area is well-ventilated. Welding fumes can be harmful if inhaled, so it is important to have a well-ventilated area to work in.
Tip 3: Keep your welder in good condition. This includes regular cleaning and maintenance. Inspect your welder before each use to make sure it is in good working order.
Tip 4: Use the correct welding technique. There are different welding techniques for different types of metals and applications. Make sure you are using the correct technique for the job at hand.
Tip 5: Be aware of your surroundings. Make sure there are no flammable materials or people in the area where you are welding.
Tip 6: Allow the welder to cool down before storing it. This will help to prevent the welder from overheating and causing a fire.
Tip 7: Store the welder in a dry place. Moisture can damage the welder, so it is important to store it in a dry place when not in use.
Tip 8: Get training from a qualified welder. If you are new to welding, it is important to get training from a qualified welder. This will help you to learn the proper techniques and safety procedures.
By following these tips, you can help to ensure that you are using industrial miller welders safely and effectively.
Summary of key takeaways or benefits:
- Following these tips can help you to use industrial miller welders safely and effectively.
- Always wear proper safety gear, make sure your work area is well-ventilated, and keep your welder in good condition.
- Use the correct welding technique, be aware of your surroundings, and allow the welder to cool down before storing it.
- Store the welder in a dry place and get training from a qualified welder if you are new to welding.
Transition to the article’s conclusion:
By following these tips, you can help to ensure that you are using industrial miller welders safely and effectively.
Conclusion
Industrial miller welders are powerful and versatile tools that are essential for a variety of industrial applications. They offer a number of benefits, including power, durability, versatility, safety, and reliability. When choosing an industrial miller welder, it is important to consider the type of welding you will be doing, the thickness of the metal you will be welding, the duty cycle you require, the safety features you need, and the budget you have.
By following the tips outlined in this article, you can help to ensure that you are using industrial miller welders safely and effectively. These welders can provide years of trouble-free service, and they can help you to get the job done right.
Youtube Video:
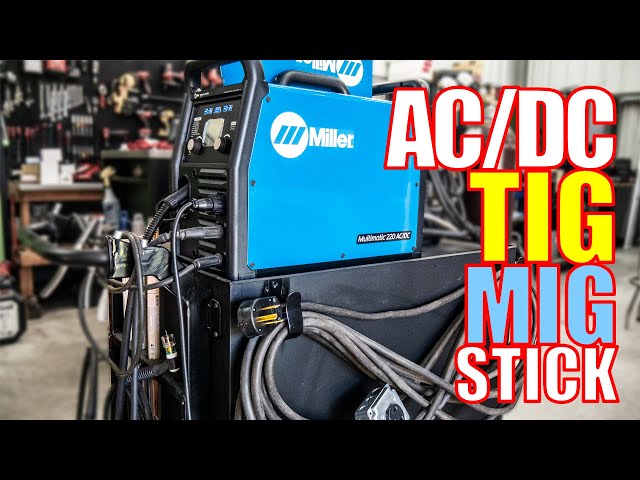