Are you in need of industrial-grade casters for your heavy-duty applications? Look no further! Industrial casters are essential components that provide mobility and support to various industrial equipment and machinery.
Editor’s Note: Industrial casters have emerged as a crucial topic in the industry today, as they play a vital role in enhancing productivity and efficiency in various sectors.
To help you make informed decisions, we’ve conducted extensive research and analysis, and put together this comprehensive guide on industrial casters. Delve into this guide to gain valuable insights and make the right choice for your specific needs.
Key Differences or Key Takeaways
Feature | Description |
Transition to Main Article Topics
Industrial Casters
Industrial casters play a critical role in various industrial applications, providing mobility, support, and functionality to heavy-duty equipment and machinery. Understanding the key aspects of industrial casters is crucial for making informed decisions and selecting the right casters for specific needs.
- Load Capacity: Determines the maximum weight the casters can support.
- Wheel Material: Impacts durability, noise levels, and suitability for different surfaces.
- Swivel Radius: Affects maneuverability and ease of movement.
- Mounting Type: Dictates how the casters are attached to equipment.
- Brake Type: Provides additional safety and stability when needed.
- Corrosion Resistance: Ensures durability in harsh environments.
- Temperature Resistance: Determines suitability for extreme temperature applications.
- Noise Level: Important for applications where noise reduction is a priority.
These key aspects are interconnected and should be carefully considered together. For instance, the load capacity and wheel material should be aligned to ensure the casters can withstand the weight and operating conditions. Similarly, the swivel radius and mounting type impact the maneuverability and stability of the equipment. By understanding these aspects and their relevance to the main topic, users can make informed decisions and select the most suitable industrial casters for their specific applications.
Load Capacity
Load capacity is a crucial aspect of industrial casters, directly impacting their ability to withstand the weight of the equipment they support. Understanding the load capacity of casters is essential to prevent overloading, which can lead to premature failure and safety hazards.
The load capacity of industrial casters is determined by various factors, including the size, material, and construction of the casters. Casters designed for heavy-duty applications typically have a higher load capacity compared to those intended for lighter loads. It is important to carefully assess the weight of the equipment and any potential dynamic forces to select casters with an appropriate load capacity.
For instance, in a manufacturing setting, heavy machinery used for lifting and transporting materials requires industrial casters with a high load capacity. These casters must be able to withstand the weight of the machinery and the load it carries, ensuring stability and safe operation. Similarly, in healthcare facilities, medical equipment such as hospital beds and MRI machines need casters with sufficient load capacity to support the weight of the equipment and patients.
Understanding the load capacity of industrial casters is critical for ensuring safety, preventing equipment damage, and maximizing the lifespan of the casters. By selecting casters with the appropriate load capacity, businesses and organizations can ensure the efficient and reliable operation of their equipment.
Factor | Impact on Load Capacity |
Wheel Material
The choice of wheel material for industrial casters significantly impacts the durability, noise levels, and suitability of the casters for different surfaces. Understanding the characteristics of various wheel materials is crucial for selecting the most appropriate casters for specific applications.
The durability of the wheel material determines its resistance to wear and tear, affecting the lifespan of the casters. For heavy-duty applications, such as in manufacturing or warehousing, casters with durable wheel materials, such as polyurethane or cast iron, are recommended to withstand demanding conditions. In environments with potential chemical exposure or extreme temperatures, casters with corrosion-resistant wheel materials, such as stainless steel or nylon, are preferred.
Noise levels are an important consideration in many industrial settings, such as healthcare facilities or office environments. Casters with noise-dampening wheel materials, such as rubber or polyurethane, can significantly reduce noise levels, creating a more comfortable and productive work environment.
The suitability of the wheel material for different surfaces is also essential. For smooth surfaces, such as finished floors or concrete, casters with hard wheel materials, such as nylon or phenolic resin, provide smooth rolling and minimize surface damage. For rough or uneven surfaces, such as gravel or outdoor terrain, casters with softer wheel materials, such as rubber or polyurethane, offer better shock absorption and traction.
Factor | Impact on Wheel Material Selection |
Understanding the connection between wheel material and the performance of industrial casters is crucial for making informed decisions and selecting the most suitable casters for specific applications. By considering factors such as durability, noise levels, and surface compatibility, businesses and organizations can optimize the performance of their equipment and ensure efficient and safe operations.
Swivel Radius
Swivel radius is a critical aspect of industrial casters that directly impacts the maneuverability and ease of movement of equipment and machinery. It refers to the angle at which the caster can swivel or rotate around its vertical axis.
-
Tight Swivel Radius:
Casters with a tight swivel radius provide excellent maneuverability in confined spaces or for applications requiring frequent directional changes. They are ideal for equipment used in warehouses, retail stores, or medical facilities, where navigating narrow aisles or maneuvering around obstacles is necessary. -
Wide Swivel Radius:
Casters with a wide swivel radius offer greater stability and are suitable for applications where straight-line movement is prioritized. They are commonly used in industrial settings, such as manufacturing plants or distribution centers, where equipment needs to move along designated paths or over long distances. -
Double Swivel Radius:
Casters with a double swivel radius provide maximum maneuverability and flexibility. They feature two swivel points, allowing the caster to rotate in multiple directions, making them ideal for equipment that requires precise positioning or frequent changes in direction. -
Swivel Lock:
Some industrial casters incorporate a swivel lock mechanism that allows the caster to be locked in a fixed position when needed. This feature provides added stability and safety, particularly for equipment used on slopes or uneven surfaces.
Understanding the connection between swivel radius and the performance of industrial casters is crucial for selecting the most suitable casters for specific applications. By considering factors such as the operating environment, frequency of movement, and required maneuverability, businesses and organizations can optimize the efficiency and safety of their equipment operations.
Mounting Type
The mounting type of industrial casters plays a crucial role in determining how they are attached to equipment and machinery. Understanding the different mounting types and their implications is essential for selecting the most suitable casters for specific applications.
-
Plate Mounting:
Plate mounting casters feature a flat plate with pre-drilled holes that allow them to be bolted directly to the equipment’s frame or base. This mounting type provides a secure and stable connection, making it suitable for heavy-duty applications and equipment that requires high load capacity.
-
Stem Mounting:
Stem mounting casters have a threaded stem that is inserted into a pre-tapped hole in the equipment’s frame. This mounting type is commonly used for lighter-duty applications and equipment that requires less load capacity. It offers a simple and cost-effective mounting solution.
-
Threaded Stem Mounting:
Threaded stem mounting casters combine the features of plate mounting and stem mounting. They have a threaded stem that is welded to a mounting plate. This mounting type provides a versatile and adjustable solution, allowing for easy installation and adjustment of the caster’s height.
-
Top Plate Mounting:
Top plate mounting casters have a mounting plate that is attached to the top of the equipment’s frame. This mounting type is commonly used for equipment that requires frequent cleaning or maintenance, as it allows the casters to be easily removed and reattached.
Selecting the appropriate mounting type for industrial casters depends on factors such as the weight of the equipment, the required load capacity, and the frequency of movement. By understanding the different mounting types and their implications, businesses and organizations can ensure that their equipment is securely and efficiently attached to industrial casters, optimizing performance and safety.
Brake Type
Industrial casters often incorporate brake mechanisms to enhance safety and stability, particularly in applications where equipment needs to be securely positioned or prevent unintended movement.
-
Locking Brakes:
Locking brakes provide a positive locking mechanism that prevents the caster from swiveling or rolling, ensuring the equipment remains stationary. These brakes are crucial in applications where stability is paramount, such as medical equipment, work platforms, or machinery used in manufacturing. -
Directional Brakes:
Directional brakes allow the caster to swivel freely but restrict movement in a specific direction. This type of brake is useful for equipment that needs to be maneuvered in confined spaces or along designated paths, such as hospital beds or industrial carts. -
Total Lock Brakes:
Total lock brakes provide the highest level of stability by simultaneously locking the swivel and wheel movement. These brakes are ideal for applications where equipment needs to be completely immobilized, such as heavy machinery or equipment used in hazardous environments. -
Foot-Operated Brakes:
Foot-operated brakes are designed to be engaged and released using a foot pedal, allowing for quick and convenient operation. These brakes are commonly used in applications where frequent locking and unlocking is required, such as mobile workstations or equipment used in production lines.
The choice of brake type depends on factors such as the required level of stability, frequency of movement, and operating environment. By incorporating the appropriate brake type, industrial casters enhance safety, prevent accidents, and ensure the efficient and reliable operation of equipment in various applications.
Corrosion Resistance
Corrosion resistance is a crucial aspect of industrial casters, particularly in applications where they are exposed to harsh environments. Harsh environments can include exposure to moisture, chemicals, salts, or extreme temperatures. Corrosion, if not adequately addressed, can lead to premature failure of the casters, compromising the safety and performance of the equipment they support.
Industrial casters with corrosion-resistant properties are designed to withstand these harsh conditions, ensuring durability and longevity. The use of corrosion-resistant materials, such as stainless steel, galvanized steel, or nylon, protects the casters from rust and other forms of corrosion. This is especially important in industries such as food processing, chemical manufacturing, or outdoor applications where exposure to corrosive elements is common.
The benefits of corrosion-resistant industrial casters extend beyond protecting the casters themselves. They also contribute to the overall safety and efficiency of the equipment they support. By preventing corrosion-related failures, these casters minimize the risk of accidents or downtime, ensuring uninterrupted operation and maximizing productivity. Moreover, corrosion-resistant casters maintain their functionality and appearance over time, reducing maintenance costs and enhancing the overall value of the equipment.
Factor | Impact on Corrosion Resistance |
Understanding the connection between corrosion resistance and industrial casters is vital for selecting the most suitable casters for specific applications. By considering the operating environment and potential exposure to harsh conditions, businesses and organizations can ensure that their equipment is supported by durable and reliable casters, maximizing performance and minimizing downtime.
Temperature Resistance
Temperature resistance is a critical aspect of industrial casters, affecting their ability to function effectively in extreme temperature environments. Extreme temperatures can occur in various industrial settings, such as manufacturing plants, warehouses, and outdoor applications. Industrial casters designed to withstand extreme temperatures are essential for ensuring the safety, reliability, and longevity of equipment in these demanding conditions.
The temperature resistance of industrial casters is determined by the materials used in their construction. Casters made from materials with high melting points and low coefficients of thermal expansion are better suited for high-temperature applications. For instance, casters made from stainless steel or high-temperature polymers can withstand elevated temperatures without compromising their structural integrity.
Conversely, industrial casters intended for low-temperature applications require materials that can maintain their strength and ductility even at sub-zero temperatures. Casters made from materials such as polyurethane or rubber are suitable for cold environments, as they exhibit good low-temperature flexibility.
The importance of temperature resistance in industrial casters cannot be overstated. Casters that are not designed for extreme temperatures can fail prematurely, leading to equipment downtime, safety hazards, and costly repairs. By selecting casters with appropriate temperature resistance, businesses and organizations can ensure that their equipment operates reliably and safely in challenging temperature conditions.
Factor | Impact on Temperature Resistance |
Understanding the connection between temperature resistance and industrial casters is crucial for selecting the most suitable casters for specific applications. By considering the operating environment and potential temperature extremes, businesses and organizations can ensure that their equipment is supported by casters that can withstand the rigors of their operating conditions, maximizing performance and safety.
Noise Level
In industrial settings, noise levels can significantly impact productivity, safety, and overall well-being. Industrial casters play a crucial role in noise reduction, contributing to a more comfortable and efficient work environment.
-
Material Composition:
The material composition of industrial casters directly influences noise levels. Casters made from materials like rubber or polyurethane provide excellent noise dampening compared to metal casters. These materials absorb vibrations and reduce rolling noise, creating a quieter work environment. -
Wheel Design:
The design of the caster wheel also affects noise levels. Casters with larger wheels tend to generate less noise than those with smaller wheels. Additionally, wheels with a wider tread pattern provide better shock absorption, further reducing noise. -
Swivel and Rotation:
The smoothness of the caster’s swivel and rotation mechanisms contributes to noise reduction. Casters with well-lubricated bearings and precision engineering minimize friction and prevent squeaking or rattling noises. -
Floor Surface:
The type of floor surface can also impact noise levels. Casters used on smooth surfaces, such as polished concrete or vinyl, tend to be quieter than those used on rough or uneven surfaces.
By understanding the connection between noise level and industrial casters, businesses can make informed decisions when selecting casters for their specific applications. Prioritizing noise reduction can create a more conducive work environment, improve employee comfort, and enhance overall productivity.
Frequently Asked Questions about Industrial Casters
Industrial casters play a crucial role in various industrial applications, and understanding their key aspects is essential for making informed decisions. This FAQ section addresses common questions and misconceptions about industrial casters to provide valuable insights and guidance.
Question 1: What is the importance of load capacity in industrial casters?
Answer: Load capacity is paramount in industrial casters as it determines the maximum weight they can support. Selecting casters with the appropriate load capacity ensures safety, prevents equipment damage, and maximizes caster lifespan.
Question 2: How does wheel material impact the performance of industrial casters?
Answer: Wheel material significantly affects durability, noise levels, and suitability for different surfaces. Choosing the right wheel material optimizes caster performance based on factors such as weight, operating environment, and surface conditions.
Question 3: What are the benefits of corrosion-resistant industrial casters?
Answer: Corrosion-resistant industrial casters are essential in harsh environments to prevent premature failure and maintain structural integrity. They protect against rust and other forms of corrosion, ensuring durability, safety, and cost savings.
Question 4: Why is temperature resistance crucial for industrial casters?
Answer: Temperature resistance ensures that industrial casters can withstand extreme temperature conditions without compromising their performance. Selecting casters with the appropriate temperature resistance prevents premature failure, equipment downtime, and safety hazards.
Question 5: How does noise level affect the selection of industrial casters?
Answer: Noise level is an important consideration for industrial casters, especially in noise-sensitive environments. Casters with noise-dampening materials and well-designed wheels minimize noise pollution, creating a more comfortable and productive work atmosphere.
Question 6: What factors should be considered when choosing the right industrial casters?
Answer: Selecting the right industrial casters involves considering factors such as load capacity, wheel material, swivel radius, mounting type, brake type, corrosion resistance, temperature resistance, and noise level. Matching caster specifications to application requirements ensures optimal performance and longevity.
We hope these FAQs have provided valuable insights into industrial casters. Understanding these aspects empowers you to make informed decisions and select the most suitable casters for your specific industrial applications.
Transition to the next article section: Types of Industrial Casters and Their Applications
Tips for Selecting and Using Industrial Casters
Industrial casters play a vital role in the functionality and safety of various equipment and machinery. To ensure optimal performance and longevity, consider the following tips when selecting and using industrial casters:
Tip 1: Determine Load Capacity:
Assess the weight of the equipment and any potential dynamic forces to determine the required load capacity of the casters. Overloading casters can lead to premature failure and safety hazards.
Tip 2: Choose Appropriate Wheel Material:
Consider factors such as durability, noise levels, and surface conditions when selecting the wheel material. Different materials, such as polyurethane, rubber, or nylon, offer unique advantages for specific applications.
Tip 3: Select the Right Swivel Radius:
Depending on the equipment’s maneuverability requirements, choose casters with a tight swivel radius for confined spaces or a wide swivel radius for straight-line movement or stability.
Tip 4: Consider Mounting Type:
Select the appropriate mounting type (e.g., plate mounting, stem mounting) based on the equipment’s design, load capacity, and frequency of movement.
Tip 5: Incorporate Brakes When Needed:
For added safety and stability, consider casters with brakes. Choose the brake type (e.g., locking, directional, total lock) that best suits the application’s requirements.
Tip 6: Ensure Corrosion Resistance:
In harsh environments, opt for corrosion-resistant casters made from materials like stainless steel or galvanized steel to prevent premature failure and maintain structural integrity.
Tip 7: Choose Temperature-Resistant Casters:
For extreme temperature applications, select casters designed to withstand high or low temperatures without compromising performance or safety.
Tip 8: Prioritize Noise Reduction:
In noise-sensitive environments, consider casters with noise-dampening materials and well-designed wheels to minimize noise pollution and create a more comfortable work atmosphere.
By following these tips, you can effectively select and use industrial casters that meet the specific requirements of your applications, ensuring optimal performance, safety, and longevity.
Transition to the article’s conclusion: Understanding the importance and considerations for industrial casters empowers you to make informed decisions and maximize the efficiency and safety of your equipment.
Conclusion
Industrial casters play a pivotal role in the efficient and safe operation of various industrial equipment and machinery. Understanding their key aspects, such as load capacity, wheel material, swivel radius, and corrosion resistance, is crucial for selecting the most suitable casters for specific applications.
By carefully considering the factors discussed in this article, businesses and organizations can optimize the performance, safety, and longevity of their equipment. Industrial casters serve as the foundation for smooth mobility, stability, and durability, contributing to increased productivity, reduced downtime, and enhanced safety in industrial environments.
Youtube Video:
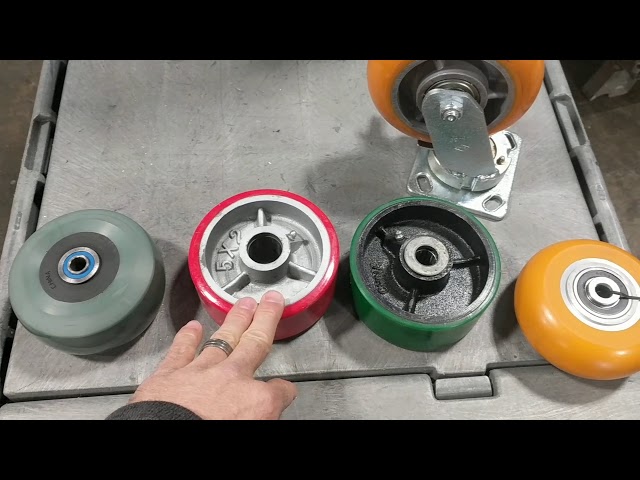